Линия LU-YH-7 (базовая комплектация)
3. Принцип работы и особенности
Основное оборудование
11. Схема ножей оборудования YH-BEJ
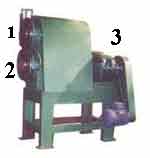
Станок предназначен для переработки автомобильных покрышек и транспортерных лент с металлическим и текстильным кордом путем разрезания их между двумя стационарными дисковыми ножами.
Диаметр перерабатываемых покрышек 12 – 24 дюйма.
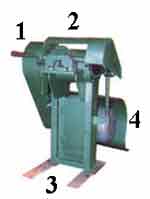
Станок предназначен для переработки "бесконечных" лент на заготовки 3х3 см, толщиной до 15 см (рекомендуемая толщина 3 – 4 см).
Состоит из:
1. Приемный механизм;
2. Режущий элемент – шестигранная звездочка;
3. Станина с электродвигателем;
4. Лоток для готовой продукции.
Состоит из:
1. Станина;
2. Механический раздвижной механизм для фиксации покрышки;
3. Штанга передвижная для режущего инструмента;
4. Режущий элемент;
5. Электрический двигатель;
6. Штурвал регулировки
7. Запорный винт
Специальные меры предосторожности
1.Во время работы станка находится не ближе трех метров, так как при обломе режущего элемента осколки могут разлететься в стороны.
2.Облом режущего элемента может произойти в результате столкновения с "щеками" раздвижного механизма.
3.Необходимо следить за жесткой фиксацией штанги перед началом работы.
4.Необходимо соблюдать общие правила электробезопасности.
5.Работать в брезентовых рукавицах во избежание порезов рук о волокна металлического корда.
Станок находится на гарантийном обслуживании в течение 1 года с момента пересечения границы КНР.
Марка | LU-YH-7 |
Единиц техники | 15 |
Наименование станков | 1. вырезатель посадочного кольца 1шт 2. разрезатель колеса на ленту 1шт. 3. разрезатель ленты на заготовки 1шт. 4. основной истирающий агрегат 1 шт 5. вибросито грубой очистки 1 шт 6. магнитный сепаратор 2 шт 7. воздушный сепаратор 1шт. 8. транспортеры 3 шт 9. электрический щит 10. вибросито тонкой очистки - 1 шт. 11. выжиматель посадочного кольца 1 шт 12. дотиратель тонкой фракции 1 шт. |
В комплектацию не входит | оборудование комплектно |
Энергопотребление номинал | 135 кВт. |
Энергопотребление реальное | 55 кВт |
Мощность главного двигателя | 43 кВт |
Расход воды | 50 литров в сутки (охлаждение) |
Потребляет сырья | 3600 кг в смену |
Производит заготовки | 3600 кг в смену ( 6 колес фуры по 65 кг в час) |
Крошка, % | 55 (0.5 - 1.0 мм) |
Пудра, % | 45 (0- 0.5 мм) |
Текстиль | удаляет |
Металл | выделяет |
Перерабатывает чистую резину | Перерабатывает |
Колеса и ленты с текстилем | Перерабатывает |
Колеса и ленты с текстилем и металлом | Перерабатывает |
Колеса с металлом | Перерабатывает |
Колеса до 4 м диаметром | Не перерабатывает |
Производительность | Зависит от содержания резины в сырье |
- в час | 200-250 кг |
-в смену 10 часов | 2000-2500 кг в смену |
-в день 22 часа | 4000-5000 кг в день |
- в год | 1200-1500 тонн |
-в смену выделяет металлолома | 1000 кг максимальное количество , завит от характеристик сырья |
-в смену выделяет текстиля | 200 кг максимальное количество , завит от характеристик сырья |
Потребляет сырья | 3000 тонн/год |
Диаметр перерабатываемых колес | 12 дюймов 24 дюйма |
Расчет режима работы | 300 дней в году, 22 часа в сутки |
Обслуживающий персонал, смена из них | 6 человек |
Квалифицированные работники | 2 |
Подсобники | 4 |
Производство разбито на участки. На каждом участке работает | 2 участка |
---Участок истирателей | 2 чел. |
---Участок подготовки колёс до 24 дюймов | 3 чел. |
Инженер-мастер – контроль процесса в целом | 1 чел. |
Вес оборудования | 10250 кг |
Сертификация оборудования | Сертифицировано КНР, Вьетнам, Монголия, Украина, Казахстан, Египет, Турция, Чехия, Израиль, Россия |
Срок заводской гарантии | 1 год |
Технические потери, % | 0,5% от массы сырья |
Производственная площадь без складов | 200 м2 |
Установка в помещении обязательна | ---участок подготовки ---участок истирания |
Установка вне помещения | нет |
Срок монтажа | 2 недели |
Выпуск фракций регулируется сменой сит | 2 фракции одновременно |
Для монтажа фундамент под оборудование | Требуется для главного истирателя |
Специалисты завода по пуско-наладке | Желателен, но не обязательно |
Обучение персонала | Желательно , но не обязательно |
Оборудование производится по лицензии | США |
Транспортировка | 1-40 футовый контейнер. |
Срок изготовления | 60 суток |
Срок отгрузки | 66 суток |
Срок доставки | 90-120 суток в зависимости от того куда везём |
ЗИП | В комплектацию не входит. |
К быстро изнашиваемым узлам относится | |
---истирающие валы 2шт | Срок службы 2 года (производство Япония) |
---дисковые ножи 2 шт | Срок службы 1 год |
---дробилка чипсов | Срок службы 1 год |
---ножи вырезателя посадочного кольца | Срок службы 4 месяца |
---барабаны выжимателя посадочного кольца | Срок службы 6 месяца (есть методика и возможность продления срока службы и реставрации ) |
---сита сменные | Срок службы 1 год |
Технология | 1.Удаление посадочного кольца------ 2. Разделение металла и резины в посадочных кольцах-------------3. Разрезание покрышки без посадочного кольца на ленту по спирали, шириной 3-5 см..------------------4. Вырезание 2-го посадочного кольца-----------5. Уменьшение толщины ленты.------------6. Нарезка заготовок (чипсов). -----------------7. Производство пудры и крошки.---------------------- 8. Разделение на фракции---------------9. Удаление текстильного корда.-------------- 10.Измельчение чистой резины (протекторных лент) и резины с текстильным кордом.------------Склад готовой продукции |
Из полученной продукции получают (крошки и пудры при дальнейшей переработке можно получит) | - регенерированную, сырую резину |
-коврики для спортивных площадок 500 х 500 мм | |
-заливные бе6сшовные покрытия с | |
-вспенивающийся каучук | |
-покрытия Новотрек | |
-подкладки под ж\д рельсы и ж.\д фурнитуру | |
-подошвы для тапочек | |
- прокладки сантехнические | |
- коврики под двери входные и коврики в ванны | |
-добавку в асфальт | |
- кровлю резиновую | |
-брусчатку резиновую | |
-гранулы ЕРДМ | |
-прокладки и уплотнители для дверей и окон | |
-протекторную ленту для восстановления колёс | |
-причальные отбойники |
1. Назначение оборудования и комплектация поставки
Данное оборудование предназначено для истирания резины, кроме того, оно может применяться для производства вторичной резиновой крошки.
Указываем основные компоненты линии YH 7-T2:
Основное оборудование
Наименование
|
Кол-во
|
Размеры (мм)
|
Основной агрегат (истиратель, вальцы)
|
1 шт.
|
3950х1800х1780
|
Вырезатель посадочного кольца
|
1 шт.
|
1900х800х1300
|
Нарезатель лент
|
1шт.
|
1250х750х1500
|
Нарезатель кусков
|
1 комплект (2 шт.)
|
700х650х1100
|
Вибросито
|
1 шт.
|
|
Вспомогательное оборудование
Наименование
|
Кол-во
|
Резиновый транспортёр
|
4 шт.
|
Электродвигатель с основанием
|
1 комплект
|
Основания под оборудование
|
4 шт. (2 больших и 2 малых)
|
Металлическая сетка
|
3 рулона (крупная, средняя и мелкая)
|
Барабан транспортёрной ленты (немного увеличенный)
|
1 шт.
|
Электрический щит
|
1 шт.
|
Мелкие детали
|
3 упаковки
|
Магнитные сепараторы
|
1 комплект (2 шт.)
|
2. Основные технические параметры
Диаметр переднего и заднего барабанов (мм)
|
400
|
Рабочая длина барабанов (мм)
|
600
|
Линейная скорость переднего барабана (м/мин)
|
17,32
|
Соотношение скоростей переднего и заднего барабанов
|
28,4
|
Отношение длины барабанов к диаметру
|
1:1,38
|
Мощность главного двигателя (кВт)
|
45
|
Обороты главного двигателя (об/мин)
|
980
|
Производительность (3-5)
|
200-300 кг/час
|
Габариты (Длина * ширина * высота)
|
3950x1800x1780
|
Масса (кг)
|
7000
|
3. Принцип работы и особенности
Станочная линия состоит из переднего и заднего барабанов, подшипников барабанов, рамы, станины, устройства регулировки зазора, предохранительных шайб, тормозной системы, системы смазки, системы трансмиссии, устройства нагрева или охлаждения, системы электрооборудования и т.д.
Вальцы – это важнейшая деталь станка. Так как при работе барабаны подвергаются сравнительно высокому давлению на их поверхность и сильному трению перетираемой резины, они изготовлены из твёрдых отливок. Поверхность барабанов ошлифована. Особенности барабанов в их высокой внутренней стойкости, сопротивлении на излом, структурной твёрдости и стойкости поверхности, высокой износостойкости. Для улучшения эффективности охлаждения, повышения отдачи при производстве резиновой крошки и качества продукта, внутренняя полость барабанов подвергается механической обработке.
Вальцы – это важнейшая деталь станка. Так как при работе барабаны подвергаются сравнительно высокому давлению на их поверхность и сильному трению перетираемой резины, они изготовлены из твёрдых отливок. Поверхность барабанов ошлифована. Особенности барабанов в их высокой внутренней стойкости, сопротивлении на излом, структурной твёрдости и стойкости поверхности, высокой износостойкости. Для улучшения эффективности охлаждения, повышения отдачи при производстве резиновой крошки и качества продукта, внутренняя полость барабанов подвергается механической обработке.
Система трансмиссии
Двигатель при помощи соединительной муфты соединён с входным валом редуктора. Вращение от редуктора при помощи муфты передаётся на задний барабан. Передний барабан приводится посредством шестерёнчатой передачи. Шестерни установлены на торце барабанов. Барабаны вращаются в разные стороны с разными линейными скоростями. Подшипники барабанов установлены на левой и правой сторонах рамы станка. Подшипник заднего барабана закреплён жёстко. Передний барабан снабжён узлом регулировки зазора между барабанами. Регулировка зазора осуществляется посредством перемещения переднего барабана в горизонтальной плоскости по направляющим рамы станка при помощи червячного регулировочного механизма. Зазор регулируется в пределах 1-8 мм. Предохранительные шайбы устанавливаются между передним концом червячного вала устройства регулировки зазора и подшипником. Предохранительные шайбы служат для обеспечения безопасности станка и оператора в случае перегрузок станка в процессе перемалывания резины, либо в результате ошибок оператора, либо в случае попадания металлических предметов между барабанами. При превышении значения несущей способности предохранительной шайбы, равной 0,7 MN, предохранительная шайба ломается, и зазор между барабанами автоматически увеличивается. При этом поперечная нагрузка на барабаны резко уменьшается, что предохраняет барабаны, раму и другие важнейшие части станка. Предохранительные шайбы изготовлены из серого литейного чугуна. Рекомендуется покупать их на заводе изготовителе для гарантии качества. Если заказчик располагает условиями для самостоятельной обработки, то ему необходимо руководствоваться соответствующими чертежами.
Рама станка
Рама станка – важнейшая деталь, которая подвержена рабочим нагрузкам. Она плотно сопрягается с верхними поперечными распорками, скрепляется болтами и образует каркас устройства. К раме крепятся подшипники барабанов. Согласно требованиям работы станка на раме установлены горизонтальные направляющие. В задней части рамы – упорная вертикальная поверхность. Эти части станка по отдельности служат для жёсткого крепления подшипников заднего барабана, изменения положения переднего барабана и для крепления механизма регулировки зазора. Рама обладает достаточной прочностью и жёсткостью, соответствует условиям эксплуатации станка и выдерживает рабочие нагрузок от вращающихся барабанов.
Подшипники барабанов
Для барабанов используются нейлоновые подшипники скольжения. Наружная деталь подшипников скольжения изготавливается из отливки. Гильза и вкладыш подшипников скольжения сопряжены статическим давлением в процессе их производства. Для внутренней поверхности подшипников скольжения использован уплотнённый нейлон марки МС. Всего в станке 6 нейлоновых подшипников скольжения, для смазки подшипников применяется смазочные масла на кальциевом основании марок ZFG3, ZFG4.
В верхней части корпуса подшипников барабана есть отверстия для смазки. Уплотнительные сальники подшипников препятствуют вытеканию смазки. Для уплотнительных колец используется специальная маслостойкая резина либо войлок. Конструкция уплотнений простая, уплотнение надёжное, обслуживание после монтажа оборудования удобное.
Устройство регулировки зазора
Устройство регулировки зазора служит для изменения положения барабанов друг относительно друга в соответствии с конкретными условиями производства резиновой крошки. Основные части устройства – ручной маховик червячного вала, червячная шестерня, диск с делениями, винты, гайки и другие детали. Устройство регулировки крепится на раме станка. При регулировке вращательное движение от ручного маховика последовательно передаётся на червячный вал, червячную шестерню, в результате чего вращение преобразуется в движение стержня по горизонтали (так как гайка жёстко закреплена на раме станка). Результат работы устройства регулировки зазора – перемещение переднего барабана в горизонтальной плоскости.
Тормозная система
Тормозная система служит для экстренной остановки станка в случае возникновения опасной ситуации по отношению к человеку либо к оборудованию. Для торможения станка применяется обратное включение электричества. Принцип работы устройства торможения: Если необходимо экстренно остановить станок, необходимо повернуть предохранительный рычаг в верхней части рамы станка. При этом замыкается путевой выключатель, прекращается подача питания на главный электродвигатель. Одновременно с этим на двигатель подаётся реверсивный импульс. Двигатель на мгновение включается в обратную сторону, благодаря чему гасится инерция вращения и он останавливается. Для обеспечения безопасности передний барабан после выключения не должен проворачиваться более чем на 1 / 4 часть длины окружности в результате инерции (Руководство по наладке электрооборудования).
Система поддержания температурного режима барабанов
Система охлаждения барабанов – открытого типа. Она отличается простой конструкцией, высокой эффективностью охлаждения, удобством контроля температуры охлаждающей жидкости (воды), низкой вероятностью образованием пробок в системе охлаждения, очень редкой возможностью её закупоривания и другими преимуществами. Принцип её работы: вода под давлением подаётся через регулировочный клапан в трубы с отверстиями для разбрызгивания, которые находятся внутри барабанов. Труба разбрызгивания имеет отверстия для воды, расположенные по всей её длине. Отверстия просверлены под прямым углом, вода орошает барабаны, и избыточное тепло при производстве резиновой крошки своевременно отводится от рабочей зоны. Вода скапливается в полости барабана и через конусный патрубок в его торцевой части сливается в водяной танк, а затем по отводной трубе сливается из станка.
18)Приводные шестерни барабанов снабжены щитками ограждения, что повышает безопасность работы, снижает риск травматизма. В случае опасности станок останавливается рычагом экстренной остановки.
Монтаж и наладочные работы.
От правильной установки станка напрямую зависят его характеристики и срок службы. В связи с этим необходимо обеспечить правильность монтажа оборудования.
Фундамент закладывается на глубину 0,85 м на основании чертежа. Работы по закладке фундамента ведутся с учётом геологических условий на месте проведения работ. Поверхность после застывания проверяется по уровню. Точность в продольной плоскости 0,2/1000, точность в поперечной плоскости 0,3/1000. Обычно фундамент закладывается в соответствии с нижеизложенной последовательностью и правилами:
Длина и ширина закладки должны быть на 200 мм. больше габаритов станины.
В соответствии с чертежами при заливке в фундаменте предусматриваются выемки для закладных болтов.
Затем выполняется заливка фундамента. Для фундамента используется цемент марки не ниже 90.
В процессе застывания фундамент в течение 7-14 дней ежедневно опрыскивается влагой.
Автомобильная покрышка заправляется в станок для вырывания посадочного кольца, фиксируется, опускается нож и вырезается посадочное кольцо №1, затем нож переносится и вырезается боковина.
Вырезание боковины рекомендуется производить для: снижения веса покрышки и снижения трудозатрат при дальнейшей переработке.
Расчетный срок исполнения операции на данном станке – 15 минут.
Переработка за час 4 покрышек от грузовиков или фур весом 65 кг.
Квалифицированный персонал обычно покрышку перерабатывает в течение 5 минут. Т.е данный станок либо работает на производство заготовок 5-6 часов в смену, либо на склад с полной загрузкой, затем 2-3 дня может не использоваться.
После этого покрышки вставляют в станок по разрезанию на ленту. Среднее время переработки 1 покрышки на данном станке указать не возможно, т.к. на старых покрышках обычно много разрезов, которые приводят к обрыву и новой заправке ленты. Кроме того на скорость работы станка влияет ширина ленты. Норматив – 3 см. Но можно нарезать и по 2 см. Тогда затраты времени возрастут, либо увеличить ширину ленты до 5 см., тогда затраты времени сократятся, но возрастут энергозатраты при истирании. На практике, оператор станка исходя из состояния покрышки и степени ее износа (толщины) определяет оптимальную ширину ленты, на которую нужно нарезать данную покрышку. Покрышка разрезается на ленту до второго посадочного кольца. Полученная лента вручную вставляется в станок для нарезания заготовок. Станок работает в автоматическом режиме и в зависимости от ширины и толщины ленты может перерабатывать в час 350 – 400 кг ленты (4-6 покрышек от фуры). Эти 3 станка имеют производительность при нормальной организации работы вдвое выше, чем истирающий агрегат, что позволяет их использовать 6-7 часов в день, при работе истирателя 22 – 23 часа/день.
Посадочные кольца вручную вставляются в станок по выжиманию металла, далее станок без участия человека их перерабатывает. Кольца вставляются по 1. Одно посадочное кольцо перерабатывается от 2-х до 4-х минут, в зависимости от количества резины на кольце и старательности оператора, работающего на станке по вырезанию посадочного кольца. Чем меньше резины, тем быстрее переработка. От диаметра посадочного кольца, структура металла так же зависит. Если металл представлен стальной проволокой, толщиной 10 – 15 мм в виде единого прута – переработка происходит медленней. Если это плетение тонких проволок, такое посадочное кольцо отделяется от резины быстрее.
Заготовки после разрезателя и резина с посадочного кольца поступают на главный транспортер истирателя и по подающему валу сбрасываются между вальцами истирающих барабанов. Производительность истирателя колеблется между 2-3 тоннами продукции в смену (10 часов).
Теоретически одна покрышка – 10 – 12 минут. Замеров времени переработки одной покрышки не проводилось в виду индивидуальности каждого случая.
В отличие от итальянской техники мы не проводим взвешивания и дозирования подачи сырья, но можем сделать на заказ. При этом цена линии значительно возрастет.
С вальцов резина поступает на вибросито грубой очистки, где разделяется на 2 фракции. Крупные куски попадают на подающий транспортер и идут на повторное перетирание.
Мелкая фракция определяется владельцем, путем установки сита нужного диаметра. На заводе обычно устанавливается стандартное сито с диаметром не больше 8 мм. Эта фракция подается транспортером на вибросито тонкой очистки. На это вибросито мелкая фракция делится на 2 части:
1) готовая продукция – фракцию определяет владелец линии путем установки сита с нужным диаметром отверстий. Из готовой фракции с помощью воздушного сепаратора удаляется текстилекорд. Далее по транспортерам последняя фракция поступает на магнитный сепаратор с постоянными не электрическими магнитами, удаляющими металлокорд, после чего готовая продукция подается на упаковку в мешки.
2) Крупная фракция, не прошедшая сита тонкой очистки, поступает на повторную переработку в вальцы. Главный истирающий агрегат гарантированно удаляет 99,5% металлокорда при нормальной настройке. В тех случаях когда перерабатываются покрышки прошедшие переработку из них гарантированно удаляется весь текстилекорд. Если перерабатываются покрышки производства Японии, КНР, марки Michelin, производства российского города Красноярск, где текстилекорд вплавлен в резину горячим способом и из тонкой фракции после истирателя продолжают торчать нитки. В этом случае продукция с текстилекордом поступает в дотиратель. Его производительность в среднем 100 кг/ч. Этот станок полностью удаляет текстилекорд из любого типа резины. Этот же станок может самостоятельно перерабатывать авиационные покрышки, автомобильные камеры, шланги и другие типы резины не содержащей металлокорда. Попадание заготовок и сырья с металлом недопустимо, т.к. чугунные диски быстро выйдут из строя (3-4 дня). Этот же станок, в тех случаях, когда с текстилекордом нет проблем, может использоваться для перетирания готовой очищенной фракции в пудру, что повышает производительность линии на 500 – 600 кг/смена. Входящий в состав линии воздушный сепаратор имеет мощность, позволяющую ему одновременно отбирать текстилекорд с двух точек, с вибросита и со станка дотирателя.
5. Монтаж оборудования
Автомобильная покрышка заправляется в станок для вырывания посадочного кольца, фиксируется, опускается нож и вырезается посадочное кольцо №1, затем нож переносится и вырезается боковина.
Вырезание боковины рекомендуется производить для: снижения веса покрышки и снижения трудозатрат при дальнейшей переработке.
Расчетный срок исполнения операции на данном станке – 15 минут.
Переработка за час 4 покрышек от грузовиков или фур весом 65 кг.
Квалифицированный персонал обычно покрышку перерабатывает в течение 5 минут. Т.е данный станок либо работает на производство заготовок 5-6 часов в смену, либо на склад с полной загрузкой, затем 2-3 дня может не использоваться.
После этого покрышки вставляют в станок по разрезанию на ленту. Среднее время переработки 1 покрышки на данном станке указать не возможно, т.к. на старых покрышках обычно много разрезов, которые приводят к обрыву и новой заправке ленты. Кроме того на скорость работы станка влияет ширина ленты. Норматив – 3 см. Но можно нарезать и по 2 см. Тогда затраты времени возрастут, либо увеличить ширину ленты до 5 см., тогда затраты времени сократятся, но возрастут энергозатраты при истирании. На практике, оператор станка исходя из состояния покрышки и степени ее износа (толщины) определяет оптимальную ширину ленты, на которую нужно нарезать данную покрышку. Покрышка разрезается на ленту до второго посадочного кольца. Полученная лента вручную вставляется в станок для нарезания заготовок. Станок работает в автоматическом режиме и в зависимости от ширины и толщины ленты может перерабатывать в час 350 – 400 кг ленты (4-6 покрышек от фуры). Эти 3 станка имеют производительность при нормальной организации работы вдвое выше, чем истирающий агрегат, что позволяет их использовать 6-7 часов в день, при работе истирателя 22 – 23 часа/день.
Посадочные кольца вручную вставляются в станок по выжиманию металла, далее станок без участия человека их перерабатывает. Кольца вставляются по 1. Одно посадочное кольцо перерабатывается от 2-х до 4-х минут, в зависимости от количества резины на кольце и старательности оператора, работающего на станке по вырезанию посадочного кольца. Чем меньше резины, тем быстрее переработка. От диаметра посадочного кольца, структура металла так же зависит. Если металл представлен стальной проволокой, толщиной 10 – 15 мм в виде единого прута – переработка происходит медленней. Если это плетение тонких проволок, такое посадочное кольцо отделяется от резины быстрее.
Заготовки после разрезателя и резина с посадочного кольца поступают на главный транспортер истирателя и по подающему валу сбрасываются между вальцами истирающих барабанов. Производительность истирателя колеблется между 2-3 тоннами продукции в смену (10 часов).
Теоретически одна покрышка – 10 – 12 минут. Замеров времени переработки одной покрышки не проводилось в виду индивидуальности каждого случая.
В отличие от итальянской техники мы не проводим взвешивания и дозирования подачи сырья, но можем сделать на заказ. При этом цена линии значительно возрастет.
С вальцов резина поступает на вибросито грубой очистки, где разделяется на 2 фракции. Крупные куски попадают на подающий транспортер и идут на повторное перетирание.
Мелкая фракция определяется владельцем, путем установки сита нужного диаметра. На заводе обычно устанавливается стандартное сито с диаметром не больше 8 мм. Эта фракция подается транспортером на вибросито тонкой очистки. На это вибросито мелкая фракция делится на 2 части:
1) готовая продукция – фракцию определяет владелец линии путем установки сита с нужным диаметром отверстий. Из готовой фракции с помощью воздушного сепаратора удаляется текстилекорд. Далее по транспортерам последняя фракция поступает на магнитный сепаратор с постоянными не электрическими магнитами, удаляющими металлокорд, после чего готовая продукция подается на упаковку в мешки.
2) Крупная фракция, не прошедшая сита тонкой очистки, поступает на повторную переработку в вальцы. Главный истирающий агрегат гарантированно удаляет 99,5% металлокорда при нормальной настройке. В тех случаях когда перерабатываются покрышки прошедшие переработку из них гарантированно удаляется весь текстилекорд. Если перерабатываются покрышки производства Японии, КНР, марки Michelin, производства российского города Красноярск, где текстилекорд вплавлен в резину горячим способом и из тонкой фракции после истирателя продолжают торчать нитки. В этом случае продукция с текстилекордом поступает в дотиратель. Его производительность в среднем 100 кг/ч. Этот станок полностью удаляет текстилекорд из любого типа резины. Этот же станок может самостоятельно перерабатывать авиационные покрышки, автомобильные камеры, шланги и другие типы резины не содержащей металлокорда. Попадание заготовок и сырья с металлом недопустимо, т.к. чугунные диски быстро выйдут из строя (3-4 дня). Этот же станок, в тех случаях, когда с текстилекордом нет проблем, может использоваться для перетирания готовой очищенной фракции в пудру, что повышает производительность линии на 500 – 600 кг/смена. Входящий в состав линии воздушный сепаратор имеет мощность, позволяющую ему одновременно отбирать текстилекорд с двух точек, с вибросита и со станка дотирателя.
5. Монтаж оборудования
В закладные отверстия устанавливаются крепёжные болты. Под станок кладутся шайбы, расстояние между ними должно быть не менее 0,5 м.
Размер шайб 150 * 150 * 25 мм.
Размер шайб 150 * 150 * 25 мм.
На фундаменте проводится осевая линия. Расхождение осевых линий станка и фундамента не может быть больше 1 мм.
Станина устанавливается по отвесу и уровню. Допустимое отклонение по осевой линии равно +/-0,02 мм / м, допуск по меридиональной плоскости +/-0,04 мм / м, допуск по высоте +/-5 мм / м.
После монтажа станины на неё устанавливается оборудование. Направляющие рельсы на двух частях рамы должны располагаться горизонтально, отклонение не может быть больше 0,08 мм. Упорная вертикальная поверхность в задней части рамы станка устанавливается на том же уровне, отклонение не может быть больше 0,08 мм. (Отклонение легко контролируется по зазорам между соединяемыми частями станка). Детали рамы плотно сопрягаются при помощи инструмента и надёжно свинчиваются. При неплотных соединениях детали подгоняются, а не соединяются при помощи прокладок. После сборки рама окончательно привинчивается к станине станка. Затем проверяется горизонтальность в плоскости А и вертикальность двух частей рамы.
Перед монтажом барабанов устанавливаются подшипники. Вкладыши подшипников должны точно совпасть с валами барабанов (совместимость поверхностей проверяется методом окрашивания). Площадь контакта вкладышей подшипников с валами барабанов должна быть не менее 70%. В случае неправильной установки детали подшипников быстро износятся. Контрольные замеры зазоров между гильзами подшипников и валами барабанов для нейлоновых вкладышей подшипников равны 0,90-1,20 мм
Затем устанавливаются редукционные шестерни барабанов (в случае если шестерни установлены на заводе, этот пункт опускается).
Барабаны свободно навешиваются, а затем крепятся на раме. Точность установки контролируется по уровню. Отклонение не может превышать 0,02 мм / м. Вслед за этим устанавливаются крышки. Зазор между подшипником и крышкой переднего барабана должен быть в пределах 0,068-0,378 мм. Зазор шеек валов барабанов с двух сторон и подшипников должен быть в пределах 2,5- 4,5 мм.
При установке редуктора и двигателя необходимо соблюдать сносность валов.
Шлицевая соединительная муфта внутренними зубьями вдевается в соединительный торцевой вал барабанов. Затем в муфту вдевается выходной вал редуктора. Расстояние между торцевыми поверхностями внутренних вкладышей обеих валов, утопленных в муфту, и краями наружной обоймы муфты должно быть 5 мм.
Вслед за этим с помощью градиометра контролируются нижеследующие замеры.
Угловое расхождение. Градиометр прижимается к шестерне заднего барабана. Опорная поверхность градиометра прижимается к торцу шлицевой муфты выходного вала редуктора. Затем валы проворачиваются (шестерня, по которой производятся замеры, проворачивается на 3 / 4 оборота, обороты шестерни, которая с ней в зацеплении не учитываются). С шагом 1 / 4 оборота показания замеряются, и вычисляется общее склонение муфты. Биение не должно превышать 0,5% радиуса муфты.
После замера биения, которое должно быть в вышеуказанных пределах (0,5%), проверяется сносность валов. Центры валов должны совпасть. Градиометр прижимается к шестерне заднего барабана. Опорная поверхность градиометра прижимается к торцу шлицевой муфты выходного вала редуктора. Затем валы проворачиваются (шестерня, по которой производятся замеры, проворачивается на 3 / 4 оборота, обороты шестерни, которая с ней в зацеплении не учитываются). С шагом 1 / 4 оборота показания замеряются, Общее отклонение не должно превышать 0,8 мм (то есть погрешность 0,4 мм).
По завершении проверки редуктор крепится к станине, и затем замеры производятся повторно. Вслед за этим крепится муфта между редуктором и электродвигателем.
При установке муфты между редуктором и электродвигателем необходимо соблюдать сносность валов. Допуски: Биение не должно превышать 0,5% радиуса муфты. Общее отклонение центров валов не должно превышать 0,4 мм (то есть погрешность 0,2 мм).
Затем последовательно устанавливаются направляющие загрузки резины (Stock guide), устройство регулировки зазора, рычаг экстренного торможения станка, защитный кожух шестерен, поддон для резины, систему смазки, систему регулировки температурного режима, другие детали и части.
При регулировке зазора между барабанами необходимо добиться малого шага регулировки (около 0,5-1 мм). Зазор должен быть равномерным по всей длине барабанов, показания на градуированном диске должны соответствовать реальному зазору.
После завершения монтажа убедитесь, что все должным образом установлено. Затем необходимо вручную провернуть на 3600 высокоскоростной вал редуктора. Убедиться, что вращение происходит без помех. После чего с помощью уровня и метра проверить контрольные обмеры, убедиться, что изменений нет. По завершении проверки, если нет замечаний, можно производить следующий этап заливки бетоном.
Марка цемента второй заливки должна быть не менее 150. Следует избегать образования лакун, наличия посторонних слоёв между двумя заливками.
После застывания цемента необходимо повторить проверку. Убедиться, что нет изменений и подтянуть винтовые соединения (Необходимо избегать изменений монтажных размеров).
Согласно инструкции по использованию электрооборудования произвести монтаж электрооборудования, выйти на заданные технические параметры.
По завершении монтажа, сборки и полной проверки оборудования необходимо выполнить контрольное проворачивание.
Подготовительные работы перед проворачиванием.
1) Проверить двигатель и электросхемы на отсутствие влаги, Проверить электрические соединения на правильность подключения и надёжность. Проверить заземление кожухов электрических устройств.
2) Проверить надёжность крепления присоединённых деталей.
3)Убрать сор, зазор между барабанами увеличить до 3-5 мм (Оба края должны быть на одинаковом расстоянии друг от друга).
4) Проверить защитные ограждения шестерён, редукторы и наличие масла в точках смазки в количестве, указанном в приложении.
5) В случае, если для подшипников барабанов применена система централизованной смазки консистентным маслом, то её регулировка и обслуживание производится согласно с приложением «Насос централизованной многоточечной смазки».
6) Убедиться, что рычаг экстренного тормоза надёжно закреплён и перемещается без помех. Проверить правильную сборку деталей устройства экстренного торможения. Проверить надёжность подсоединений тяг устройства торможения. Проверить все шарниры.
7) Проверить работу устройства поддержания температурного режима (Температура воды должна быть около 100С, охлаждающая вода не должна содержать солевых примесей).
8) После завершения проверки вручную провернуть выходной вал редуктора. Убедиться, вращение свободное в двух направлениях, нет помех и ничего необычного. После этого можно включать масляный насос. Дождаться, когда давление масла придёт в норму, и масломерные стёкла покажут наличие масла в подшипниках. Включить двигатель, убедиться, что вал вращается в нужную сторону, барабаны крутятся друг навстречу другу. Недопустимо менять подключение фаз электродвигателя.
Проверка на холостом ходу.
Проверка на холостом ходу производится по завершении предварительной проверки и при её положительном результате. Время проверки на холостом ходу не менее 4-х часов.
1)Добавить масла до нужного уровня и запустить станок.
2) Проверить стабильность работы, отсутствие необычных звуков, вибраций, отсутствие слабины в соединениях. Шум должен быть не выше 83 ДБ (А).
3) Проверить электрический ток двигателя (Мощность не превышает 20% номинальной).
4) Проверить систему экстренного торможения потянув рычаг 2-3 раза (Интервал между испытаниями не менее 5 мин). Необходимо, чтобы обратное вращение переднего барабана было не более 1 / 4 радиуса барабана.
5) Вращение барабанов нормальное, без рывков и задержек.
6) Подшипники барабанов не должны нагреваться, их температура должна быть не выше 200С.
7) В подшипниках барабанов, редуктора, шестерён и в других точках смазки должно быть достаточное количество масла, Крышки подшипников, соединения, точки смазки, заглушки не должны пропускать масло.
8) Проворачивание с нагрузкой.
Проворачивание с нагрузкой производится по завершении проверки на холостом ходу и при её положительном результате.
9) При произведении проверки с нагрузкой вначале необходима минимальная загрузка, затем нагрузка увеличивается. Вначале применяется мягкий материал, затем жёсткий. Этапы проверки:
Первый этап: Нагрузка 20-50% от номинальной мощности, время проверки 16 часов.
Второй этап: Нагрузка 50-75% от номинальной мощности, время проверки 16 часов.
Третий этап: Нагрузка 100% номинальной мощности, время проверки 8 часов.
Во время проверки контролируются нижеследующие показатели.
Температура узлов не должна сильно расти, температура подшипников редуктора, корпусов подшипников
не должна превышать нижеуказанную.
Узел
|
Температура (0С)
|
Максимум температуры (0С)
|
Нейлоновые подшипники
|
35
|
65
|
Подшипники редуктора
|
40
|
70
|
Нагрузка не должна превышать номинальной мощности электродвигателя (Допустимо превышение на короткий промежуток времени).
В случае если при испытаниях в подшипниках будет недостаточно масла, подшипники станут греться, появятся сильные вибрации, нагрузка на превысит разрешённую, возникнут другие нештатные ситуации, то необходимо остановить испытания, выяснить причину, устранить неполадки и снова начать испытания.
Что следует помнить оператору
При испытаниях и эксплуатации оборудования необходимо обращать внимание на нижеследующие пункты, для того, чтобы обеспечить нормальную работу оборудования.
1) Перед запуском необходимо отрегулировать зазор, для того чтобы не повредить барабаны и не допустить обугливания.
2) Во время регулировки барабанов необходимо следить, чтобы зазор между двумя противоположными торцами барабанов был равномерным. В противном случае будут повреждены шестерни и другие детали.
3) Перед запуском необходимо проверить уровень масла.
4) Вальцы нагреваются и охлаждаются при вращении, во избежание температурного коробления барабанов. По окончании работы необходимо дождаться, когда барабаны охладятся до 500С, и только после этого разрешается остановить станок.
5) Когда станок используется для производства резиновой крошки, резина предварительно подогревается и измельчается. Когда в станок загружаются куски резины весом более 5 кг, то загрузка производится со стороны шестерён.
6) Необходимо определённое время проработать на холостом ходу. Проверить надёжность и лёгкость работы экстренного тормоза. Не пользоваться тормозом для остановки станка, если в этом нет крайней необходимости.
7) Не допустимо включение двигателя, когда станок загружен.
8) Перед запуском станка необходимо убедиться в надёжном креплении всех деталей, в комплектности и целостности защитных щитков. Проверить масломерные стёкла, маслёнки и точки смазки редуктора, убедиться, что водяной контур и все другие приборы надёжно функционируют.
9) Необходимо регулярно проверять наличие смазки в подшипниках барабанов.
Когда используется система смазки консистентным маслом, необходимо своевременно пополнять точки смазки.
10) После продолжительной эксплуатации оборудования заглушки подшипников из-за износа могут пропускать масло. Если утечка масла продолжается и после того, как заглушки будут подтянуты, то необходимо их снять и убрать уплотнительные кольца. Затем крышки уплотняются войлоком либо иным уплотнительным материалом. Концы уплотнительной полосы обрезаются под углом 450. Полоса укладывается в кольцо так чтобы концы оказались друг под другом и зажимается заглушкой.
11) Если из-за повышенных нагрузок сломалась предохранительная шайба, то необходимо остановить двигатель и заменить шайбу. Последовательность операций по замене шайбы:
12) Отдать винты состыкованного узла, снять одну его половину.
13) Повернуть маховик устройства регулировки зазора между барабанами, чтобы червячный стержень дал ход назад, и снять предохранительную шайбу.
14) Заменить предохранительную шайбу. Повернуть маховик устройства регулировки зазора и добиться равновесия узла с установленными на нём противовесами. Установить половинку состыкованного узла, затянуть винты.
15) Необходимо, чтобы зазоры между противоположными концами барабанов были одинаковыми при их регулировке. При изменении зазора необходимо сравнивать величину реального зазора с показаниями на градуированном диске и своевременно исправлять погрешность. Исправление погрешности в особенности необходимо после замены предохранительной шайбы.
16) Устройством экстренной остановки станка необходимо пользоваться только при возникновении экстренной ситуации. Для того, чтобы гарантировать надёжность его работы, необходимо проводить регулярные проверки устройства. После поворота рычага устройства экстренной остановки станка передний барабан по инерции делает не более 1 / 4 оборота. Если показатели не в норме, необходимо выполнить регулировки согласно с инструкцией для электрооборудования станка.
17) В случае если возникла неисправность вставки подшипника, не следует останавливать станок. Необходимо немедленно его разгрузить и оставить на холостом ходу до прихода специалиста.
18) Запрещено включать загруженный станок.
19) Когда при ремонте станка необходимо снять шестерни, нужно убрать клиновую шпонку. Для демонтажа шпонки рекомендуется руководствоваться рисунком 18 (Приложен другой рисунок). Последовательность операций замены клиновой шпонки:
20) Изготовить съёмник для шпонки (Можно использовать подходящий металлический профиль в виде жёлоба).
21) Вкрутить винт в отверстие у хвоста клиновой шпонки, поставить на винт съёмник и вкрутить гайку.
22) Провернуть гайку ключом пока шпонка не начнёт отходить. Когда усилие на шпонке полностью ослабнет, снять её руками. При этом:
23) Запрещается ударять по шестерне и по шпонке молотком, применять иные методы, которые могут повредить детали станка.
24) В нормальных условиях необходимо проводить регулярное техническое обслуживание станка. Согласно с видами обслуживания оценивается износ комплектующих и их надёжность, изношенные детали восстанавливаются либо заменяются. Проверяется зазор между шейкой вала барабанов и вкладышем подшипника, когда зазор больше 1,2 мм, вкладыш подшипника заменяется.
7. Перечень точек смазки
Основные смазываемые узлы | Рекомендуемая смазка | Заменитель | Кол-во закладываемого масла | Периодичность замены | ||
Наименование | Тип | Наименование | Тип | |||
Подшипники барабанов
|
Масло на кальциевой основе
|
ZN-2
|
Масло на натриево-кальциевой основе
|
ZGN-2
|
3-я кольцевая насечка масляного стакана
|
1 раз в смену
|
Подшипники промежуточного вала редуктора
|
Масло на кальциевой основе
|
ZN-2
|
Масло на натриево-кальциевой основе
|
ZGN-2
|
3-я кольцевая насечка масляного стакана
|
1 раз в смену
|
Редуктор
|
Промышленное трансмиссионное масло
|
N150
|
Моторное масло
|
#11
|
По норме
|
Дозаправка масла раз в сезон, раз в год замена масла
|
Шестерни привода вальцов
|
Масло для открытых шестерёнчатых передач
|
68
|
Промышленное трансмиссионное масло
|
N68
|
Поддерживать обильное наличие масла на шестернях
|
|
Регулировочный узел
|
Масло на натриевой основе
|
ZN-2
|
Масло на натриево-кальциевой основе
|
ZGN-2
|
Достаточное кол-во
|
Дозаправка масла раз в сезон
|
8. Подшипники
№ п/п
|
Наименование подшипников
|
Тип
|
Размеры
|
Кол-во
|
Место установки
|
||
d | D | b | |||||
1
|
Двурядные шариковые подшипники
|
53520
|
100
|
180
|
46
|
1
|
Вал привода шестерён
|
2
|
Однорядные упорные шариковые подшипники
|
8106
|
30
|
47
|
11
|
4
|
Червячный редуктор узла регулировки
|
9. Быстроизнашивающиеся части
№ п/п
|
Тип
|
Наименование
|
Кол-во
|
Материал
|
Примечание
|
1
|
000103
|
Эластичные кольца
|
40
|
Резина
|
Рис. 5
|
2
|
020039
|
Предохранительные шайбы
|
2
|
НТ150
|
Рис. 4
|
10. Основные неисправности и способы их устранения
Узел и неисправность
|
Причина
|
Устранение
|
Повышенная вибрация и повышенная шумность станка
|
1. Ослаблен резьбовой крепёж
2. Большой зазор между гильзами подшипников и рамой станка
3. Износ шестерён привода истирающих барабанов
|
1. Затянуть крепёж
2. Вставить шайбы
3. Заменить шестерни
|
Температура подшипников барабанов выше 650С
|
1. Неправильно установлен зазор между истирающими вальцами
2. Недостаточная смазка
3. Неправильный монтаж
4. Износ гильзы либо вкладыша подшипника
5. Недостаточное охлаждение вальцов
|
1. Установить зазор в соответствии с нормами
2. Заменить масло
3. Собрать детали заново
4. Отремонтировать либо заменить
5. Улучшить работу системы охлаждения
|
Высокая шумность редуктора
|
1. Неправильное зацепление шестерён
2. Люфт шестерни на валу
3. Износ подшипников
|
1. Отрегулировать и приработать шестерни
2. Отремонтировать либо заменить
3. Заменить подшипники
|
Температура подшипников редуктора выше 650С
|
1. Плохая смазка
2. Неправильные зазоры
3. Износ подшипников
4. Несовпадение валов либо их несносность
|
1. Улучшить работу системы смазки
2. Отрегулировать зазоры
3. Заменить подшипники
4. Ремонт либо замена
|
Время экстренной остановки барабанов превышает нормированное
|
Плохая работа колодок экстренного тормоза
|
Отрегулировать либо заменить
|
Частый выход из строя предохранительных шайб
|
1. Качество или размеры предохранительных шайб не соответствуют требованиям
2. Непараллельность валов, неправильный зазор
|
1. Заменить предохранительные шайбы
2. Отрегулировать в соответствии с требованиями
|
11. Схема ножей оборудования YH-BEJ
![]() |
Нож измельчителя |
![]() |
Нож нарезателя |
![]() |
Нож вырезателя кольца |
12. Схема размещения технологического оборудования



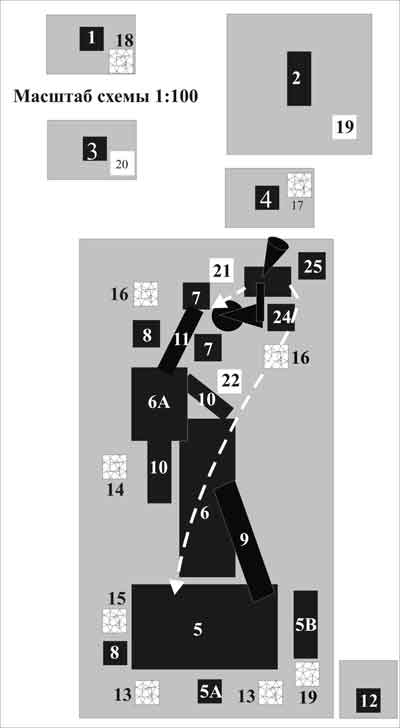
13. Станок для разрезания автопокрышки на «бесконечную» ленту



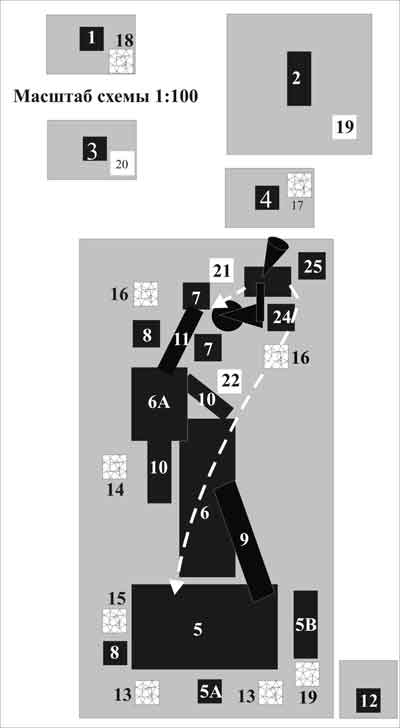
Проектная площадь цеха - 300 м 2 12 м - шир., 18 м - дл., 5 м - выс. цеха
Фундамент требуется агрегату № 6.
Схема размещения рекомендована. Жёстких ограничений по проекту относительно размещения станков друг друга нет.
Площадь зон безопасности рекомендована для всех станков (кроме № 2).
Для станка №2 - 2м зона безопасности обязательна
1 - Щит электрический
2 - Горизонтальный вырезатель посадочного кольца
3 - Дисковый разрезатель покрышки на ленту
4 - Дробилка ленты на заготовку
5 - Основной истирающий агрегат
6 - Вибросито третьего класса
6А - Вибросито тонкой очистки
7 - Магнитные сепараторы(2 шт.)
8 - Место возможной установки магнитного сепаратора
9 - Транспортёр для подачи сырья в истирающий агрегат и повторного истирания крупной фракции
10 - Транспортёры подачи крупной и мелкой фракции на магнитные сепараторы
11 - Транспортёры подачи готовой продукции 2 разных фракций одновременно
12 - Ёмкость на 50 - 100 л с чистой водой для охлаждения основного истирающего агрегата
13 - Зоны регулировки истирающих агрегатов
14 - Зоны сбора и складирования металлокорда
15 - Зоны сбора и складирования текстилекорда
16 - Зоны сбора и складирования готовой продукции
17 - Зона заправки ленты в дробилку
18 - Зона обслуживания электрощита
19 - Зона постоянного нахождения рабочего на вырезке посадочных колец
20 - Зона постоянного нахождения рабочего на разрезателе ленты
21 - Зона постоянного нахождения рабочего на подаче сырья
22 - Зона постоянного нахождения рабочего на контроле выхода продукции
23 - Зона постоянного нахождения рабочего на упаковке готовой продукции
24 - Дополнительный истиратель для удаления текстилекорда
25 - Воздушный сепаратор
13. Станок для разрезания автопокрышки на «бесконечную» ленту
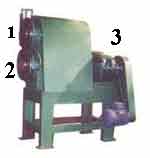
Станок предназначен для переработки автомобильных покрышек и транспортерных лент с металлическим и текстильным кордом путем разрезания их между двумя стационарными дисковыми ножами.
Диаметр перерабатываемых покрышек 12 – 24 дюйма.
Состоит из:
1. Дисковый нож верхний;
2. Дисковый нож верхний;
3. Корпус с электродвигателем внутри.
2. Дисковый нож верхний;
3. Корпус с электродвигателем внутри.
Метод использования
Покрышка с удаленным посадочным кольцом вставляется между дисковыми ножами тем бортом, где нет кольца. Станок включается. При работе покрышку необходимо поддерживать на весу или использовать подставку. Станок может резать резину толщиной до 15 см (резина, снятая с изоляции подводных лодок и покрышек самолетов). Ширина получаемой ленты может колебаться от 2,5 до 7 см. Регулируется путем синхронного смещения обоих дисковых ножей на нужное расстояние. Рекомендуемый, наиболее экономичный, зазор 3 – 3,5 см. На этот уровень станок настроен первоначально. Расчетный срок переработки одной покрышки диаметром 24 дюйма – 4-5 мин.
Примечание 1: фундамент при установке не требуется.
Примечание 2: моторесурс ножей рассчитан на 1 год. Правка и заточка ежемесячно, полная
замена – ежегодно.
Покрышка с удаленным посадочным кольцом вставляется между дисковыми ножами тем бортом, где нет кольца. Станок включается. При работе покрышку необходимо поддерживать на весу или использовать подставку. Станок может резать резину толщиной до 15 см (резина, снятая с изоляции подводных лодок и покрышек самолетов). Ширина получаемой ленты может колебаться от 2,5 до 7 см. Регулируется путем синхронного смещения обоих дисковых ножей на нужное расстояние. Рекомендуемый, наиболее экономичный, зазор 3 – 3,5 см. На этот уровень станок настроен первоначально. Расчетный срок переработки одной покрышки диаметром 24 дюйма – 4-5 мин.
Примечание 1: фундамент при установке не требуется.
Примечание 2: моторесурс ножей рассчитан на 1 год. Правка и заточка ежемесячно, полная
замена – ежегодно.
Специальные меры предосторожности
1. Соблюдать общие правила электробезопаности. Обязательно заземление станка.
2. Так как персонал будет постоянно находится в непосредственном контакте с механизмом, необходимо следить за возможностью попадания между дисковыми ножами верхних конечностей и фаланг пальцев персонала.
3. Рекомендуется работать в металлических кольчужных перчатках .
4. При заклинивании станка в процессе разрезания, он высвобождается путем подачи заднего хода.
5. Не допускать перенастройку станка и снятие ограничителей со скорости вращения дисковых ножей.
6. Колесо режется на "бесконечную" ленту пока до второго посадочного кольца не останется 4-5 см.
Станок находится на гарантийном обслуживании в течение 1 года с момента пересечения границы КНР.
1. Соблюдать общие правила электробезопаности. Обязательно заземление станка.
2. Так как персонал будет постоянно находится в непосредственном контакте с механизмом, необходимо следить за возможностью попадания между дисковыми ножами верхних конечностей и фаланг пальцев персонала.
3. Рекомендуется работать в металлических кольчужных перчатках .
4. При заклинивании станка в процессе разрезания, он высвобождается путем подачи заднего хода.
5. Не допускать перенастройку станка и снятие ограничителей со скорости вращения дисковых ножей.
6. Колесо режется на "бесконечную" ленту пока до второго посадочного кольца не останется 4-5 см.
Станок находится на гарантийном обслуживании в течение 1 года с момента пересечения границы КНР.
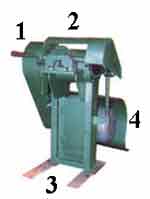
Станок предназначен для переработки "бесконечных" лент на заготовки 3х3 см, толщиной до 15 см (рекомендуемая толщина 3 – 4 см).
Состоит из:
1. Приемный механизм;
2. Режущий элемент – шестигранная звездочка;
3. Станина с электродвигателем;
4. Лоток для готовой продукции.
Метод использования
"Бесконечная" лента вставляется в приемник станка, станок включается. Разрезание ленты и выброс заготовок происходит автоматически, поэтому постоянное присутствие персонала не требуется. Необходимо только вручную подавать новую ленту и затаривать заготовки. Станок сам затягивает ленту после того, как она вставлена Время разрезания ленты одного колеса - 4 – 5 минут.
В случае заклинивания или перегруза станка, он возвращается в рабочее состояние путем подачи обратного хода.
Примечание 1: фундамент при установке не требуется.
Примечание 2: заточка режущего инструмента – шестигранной звездочки – производится 2 раза в
месяц, норматив службы – 6 месяцев.
"Бесконечная" лента вставляется в приемник станка, станок включается. Разрезание ленты и выброс заготовок происходит автоматически, поэтому постоянное присутствие персонала не требуется. Необходимо только вручную подавать новую ленту и затаривать заготовки. Станок сам затягивает ленту после того, как она вставлена Время разрезания ленты одного колеса - 4 – 5 минут.
В случае заклинивания или перегруза станка, он возвращается в рабочее состояние путем подачи обратного хода.
Примечание 1: фундамент при установке не требуется.
Примечание 2: заточка режущего инструмента – шестигранной звездочки – производится 2 раза в
месяц, норматив службы – 6 месяцев.
Специальные меры предосторожности
1. Соблюдать общие правила электробезопасности.
2. Необходимо следить за возможностью попадания в приемный механизм верхних конечностей и фаланг пальцев персонала.
3. Рекомендуется работать в кольчужных перчатках.
4. Запрещается самовольная регулировка скорости работы режущего элемента.
5. Запрещается замена шестигранного элемента на восьми- и девятигранные.
6. Замена их на четырех- и пятигранные допустима.
Станок находится на гарантийном обслуживании в течение 1 года с момента пересечения границы КНР.
1. Соблюдать общие правила электробезопасности.
2. Необходимо следить за возможностью попадания в приемный механизм верхних конечностей и фаланг пальцев персонала.
3. Рекомендуется работать в кольчужных перчатках.
4. Запрещается самовольная регулировка скорости работы режущего элемента.
5. Запрещается замена шестигранного элемента на восьми- и девятигранные.
6. Замена их на четырех- и пятигранные допустима.
Станок находится на гарантийном обслуживании в течение 1 года с момента пересечения границы КНР.
15. Станок для горизонтального вырезания посадочного кольца (разрезание покрышки по кругу)
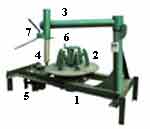
Станок предназначен для переработки автомобильных покрышек диаметром от 12 до 24 дюймов с металлическим и текстильным кордом.
Состоит из:
1. Станина;
2. Механический раздвижной механизм для фиксации покрышки;
3. Штанга передвижная для режущего инструмента;
4. Режущий элемент;
5. Электрический двигатель;
6. Штурвал регулировки
7. Запорный винт
Метод использования
С помощью штурвала (6) устанавливается необходимый размер в раздвижном механизме (2), надевается покрышка и закрепляется в станке с помощью штурвала. Штанга (3) с укрепленным в ней режущим элементом (4) подносится к покрышке и фиксируется с помощью винта (7). Включается электрический двигатель (5). После 20 витков разрезание завершено, и посадочное кольцо удаляется. Штанга возвращается в исходное положение. Раздвижной механизм ослабляется штурвалом. Разрезанная покрышка без посадочного кольца снимается и отправляется на дальнейшую переработку.
Примечание: при двухсменной работе заточка режущего инструмента производится каждые 2 недели, полная замена – раз в полгода.
С помощью штурвала (6) устанавливается необходимый размер в раздвижном механизме (2), надевается покрышка и закрепляется в станке с помощью штурвала. Штанга (3) с укрепленным в ней режущим элементом (4) подносится к покрышке и фиксируется с помощью винта (7). Включается электрический двигатель (5). После 20 витков разрезание завершено, и посадочное кольцо удаляется. Штанга возвращается в исходное положение. Раздвижной механизм ослабляется штурвалом. Разрезанная покрышка без посадочного кольца снимается и отправляется на дальнейшую переработку.
Примечание: при двухсменной работе заточка режущего инструмента производится каждые 2 недели, полная замена – раз в полгода.
Специальные меры предосторожности
1.Во время работы станка находится не ближе трех метров, так как при обломе режущего элемента осколки могут разлететься в стороны.
2.Облом режущего элемента может произойти в результате столкновения с "щеками" раздвижного механизма.
3.Необходимо следить за жесткой фиксацией штанги перед началом работы.
4.Необходимо соблюдать общие правила электробезопасности.
5.Работать в брезентовых рукавицах во избежание порезов рук о волокна металлического корда.
Станок находится на гарантийном обслуживании в течение 1 года с момента пересечения границы КНР.
16. Схемы устройств и механизмов комплекса LU-YH 7
Рис. 1: Основное устройство
![]() |
1. Направляющие пластины для загрузки измельчённой резины 2. Масломерное стекло 3. Устройство экстренной остановки 4. Подшипник 5. Устройство регулировки температуры вала 6. Резервуар для воды 7. Барабан 8. Станина 9. Поддон для крошки 10. Кожух рамы 11. Устройство регулировки зазора 12. Кожух шестерен барабанов 13. Система смазки жидким (консистентным) маслом 14. Планетарный редуктор 15. Ограждение муфты 16. Главный двигатель |
Рис. 2: Схема трансмиссии
![]() |
1. Главный двигатель 2. Соединительная муфта 3. Планетарный редуктор 4. Соединительная муфта 5. Шестерни барабанов с разной скоростью вращения 6. Устройство регулировки зазора 7. Передний барабан 8. Задний барабан 9. Роликовый подшипник |
Рис. 3: Подшипник барабана (Нейлоновая гильза подшипника)
![]() |
Рис. 4: Схема уплотнительных конструкций подшипников переднего и заднего барабанов ![]() |
Рис. 5: Перепускной клапан
![]() |
Рис. 6: Уплотнительное кольцо
![]() ![]() |
Рис. 7: Съёмник клиновой шпонки
![]() |
Рис. 8: Балансир
![]() |
Рис. 9: Эластичная трубка
![]() |